In the wood processing industry, your equipment is like a trusty sidekick. The smoother it runs, the better your work goes! However, as time goes on, these helpers can run into some hiccups. To keep your wood processing equipment in top shape, regular maintenance is a must! Let’s explore some simple and fun maintenance tips to help extend your equipment’s “lifespan.”
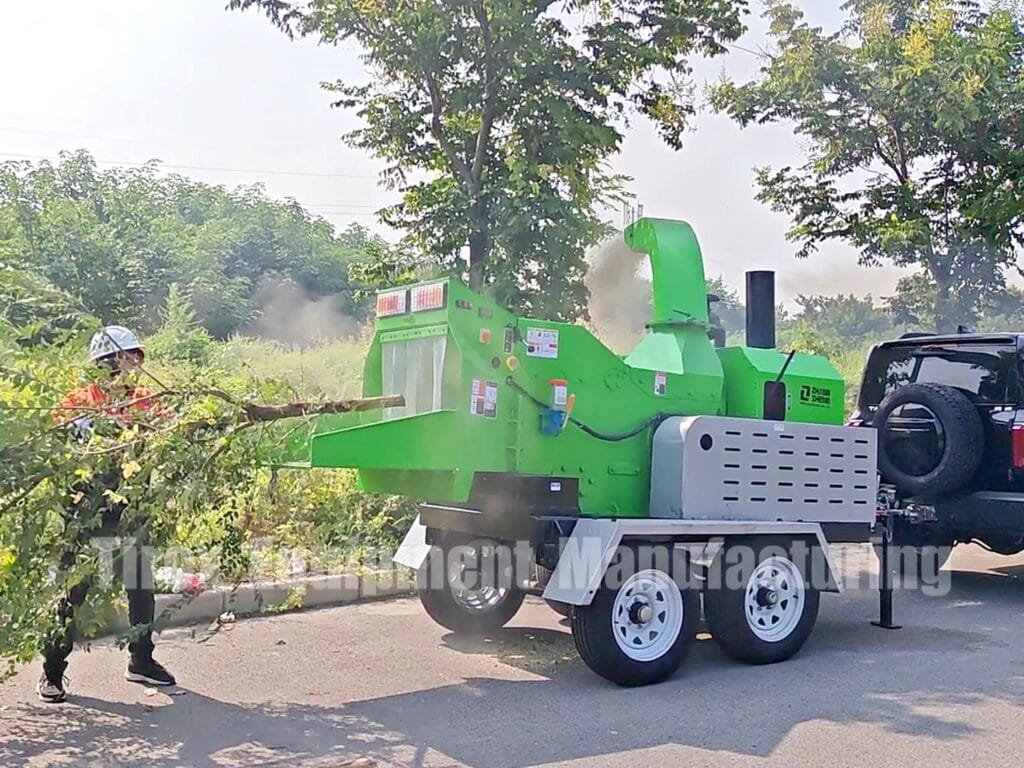
Regular Check-Ups and Care
Imagine if your equipment could have a little check-up before every job—how great would that be? Regular checks help you spot potential issues before they become big problems. Spend some time each month focusing on these key areas:
- 1.Blade Wear: The blades are like your equipment’s “teeth.” If they get dull, cutting won’t be as effective. Check the blades regularly to make sure they’re sharp. If they’re worn out, replace them!
- 2.Lubrication System: Keeping the lubrication system running smoothly is like giving your equipment a drink. It reduces friction and helps everything work better. Don’t forget to check the oil levels and quality to avoid dryness.
- 3.Electrical System: Regularly check the electrical connections to ensure nothing is loose or corroded, preventing any unexpected shutdowns.
Cleaning the Equipment
Cleaning your equipment isn’t a chore; it’s a way to keep it happy! Wood processing machines create a lot of wood chips and resin during work, and these need to be cleaned up! Here’s how you can do it:
- 1.Daily Cleaning: After each use, grab a broom or a cloth and clean off any wood chips and dust. Keeping everything tidy helps your equipment feel fresh.
- 2.Deep Cleaning: Every so often, do a deep clean, especially around the blades and feed openings. Pick a time when the equipment isn’t busy to give it a thorough scrub.
Lubrication and Parts Replacement
If you want your equipment to run smoothly, lubrication is key! Think of it as putting “slippery oil” on your equipment—it helps everything glide along. Also, keep an eye on replacing important parts:
- 1.Blades: Regularly check the blades and replace them when they’re too worn. This keeps cutting at its best.
- 2.Belt and Other Parts: Check belts regularly, and replace any that are worn. This prevents small issues from causing downtime. Using original parts is a smart choice to ensure compatibility and performance.
Operator Training
Maintaining the equipment isn’t just up to you; training your operators is important too! Good training helps prevent damage from mistakes and makes sure everyone knows how to use the machines well. Training can include:
- 1.Correct Operating Methods: Ensure everyone understands how to operate the equipment properly to avoid unnecessary hassles.
- 2.Common Issue Handling: Teach operators how to spot common problems and how to fix them.
Keeping Maintenance Records
Maintenance records are like a “growth diary” for your equipment, helping you keep track of its “health.” It’s a good idea to record the following:
- 1.Maintenance Dates: Write down when maintenance was done for easy reference.
- 2.Parts Replaced: Keep track of any parts replaced and when, to understand their lifespan.
- 3.Inspection Results: Note any issues found during checks and how you resolved them for future reference.
Conclusion
In short, regular maintenance of your wood processing equipment not only boosts efficiency but also helps your equipment last longer. By following these simple maintenance tips, you’ll find your equipment stays in great shape and experiences fewer problems, making your work smoother. So, take action now and give your wood processing equipment a healthy and happy “life”!